5 Steps to Build Your Own DIY Automatic Hydroponic Nutrient Doser
Creating a DIY automatic hydroponic nutrient doser entails precise integration of dosing pumps, nutrient reservoirs, and advanced control systems for ideal fertigation. Key components include high-quality peristaltic or diaphragm pumps, reliable pH and electrical conductivity (EC) sensors, and robust microcontrollers like Arduino or Raspberry Pi to automate dosing schedules.
Essential steps involve calibrating pumps for accurate nutrient delivery, programming appropriate schedules for different growth stages, and ensuring real-time monitoring and adjustments to maintain stable nutrient concentrations. Regular maintenance and troubleshooting are crucial to prevent imbalances and achieve consistent plant health.
Discover how to master these elements and enhance your hydroponic system's efficiency.
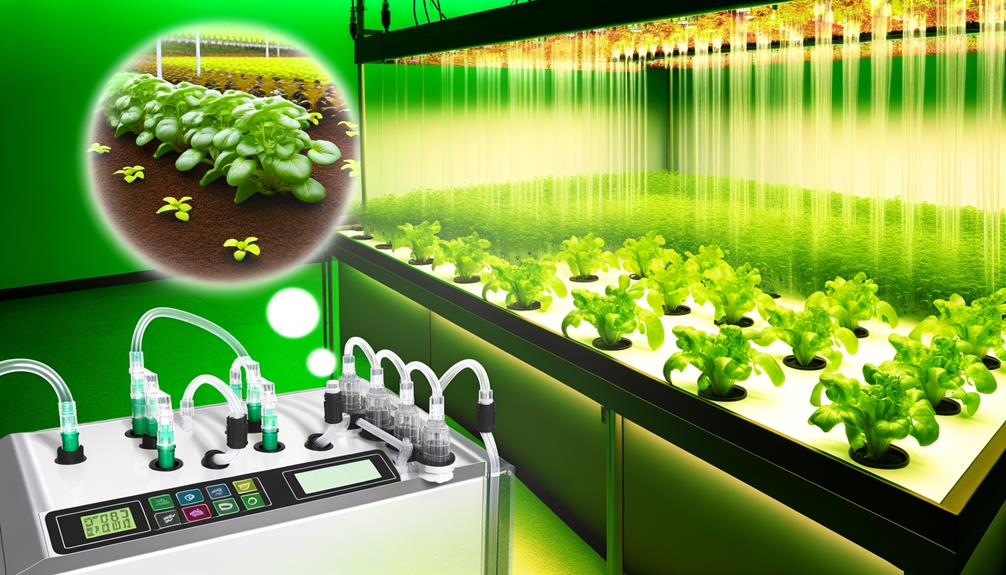
Key Takeaways
- Utilize peristaltic dosing pumps to ensure precise and consistent nutrient delivery.
- Integrate microcontrollers like Arduino or Raspberry Pi for automated control.
- Employ pH and EC sensors for real-time monitoring and adjustments.
- Program dosing schedules tailored for different growth stages: seedling, vegetative, flowering.
Understanding Hydroponic Nutrient Dosing

Hydroponic nutrient dosing, frequently referred to as fertigation, is a vital process that involves the precise delivery of essential nutrients to plants through a water-based solution.
This method guarantees that plants receive a balanced mix of macro and micronutrients, important for peak growth and yield. Key components include nitrogen, phosphorus, potassium, calcium, magnesium, and trace elements like iron and manganese.
In hydroponic systems, nutrient concentration and pH levels must be meticulously monitored and adjusted. Electrical conductivity (EC) meters and pH sensors are commonly employed to maintain ideal conditions.
Accurate dosing schedules and formulations are necessary to prevent nutrient imbalances, which can lead to deficiencies or toxicities. Mastery of fertigation techniques is fundamental for successful hydroponic cultivation.
Benefits of Automatic Dosing
Implementing an automatic dosing system in hydroponic setups guarantees precise and consistent nutrient delivery, optimizing plant health and growth by maintaining balanced nutrient concentrations.
This automation considerably reduces manual intervention, providing time-saving convenience for growers and allowing for more efficient resource management.
Additionally, it minimizes human error, thereby enhancing the reliability and scalability of hydroponic operations.
Consistent Nutrient Delivery
By utilizing automatic nutrient dosing systems, growers can achieve unparalleled consistency in nutrient delivery, thereby improving plant health and maximizing yield potential.
These systems precisely calibrate the concentration of essential macro and micronutrients in the hydroponic solution, ensuring a stable pH and Electrical Conductivity (EC) range. This mitigates the risk of nutrient imbalances, which could lead to deficiencies or toxicities that impede growth.
Automated dosers employ sensors and controllers to continuously monitor and adjust nutrient levels, facilitating a uniform distribution of nutrients across all growth stages.
This precision is critical for maintaining ideal metabolic processes, enhancing photosynthesis, and promoting robust root development.
Consequently, plants exhibit more predictable growth patterns, resulting in higher productivity and superior crop quality.
Time-Saving Convenience
Automated nutrient dosing systems provide substantial time-saving advantages by eliminating the need for manual nutrient mixing and adjustment, thereby allowing growers to focus on other critical aspects of crop management.
This technology enhances operational efficiency by ensuring precise delivery of nutrients, mitigating human error, and optimizing resource utilization. The integration of automated systems can result in significant labor cost reductions and improved crop outcomes.
- Enhanced productivity: Redirect labor towards more strategic tasks.
- Consistency: Minimize variability in nutrient application.
- Scalability: Easily manage larger operations without proportional increases in labor.
- Reliability: Reduce the risk of human error in nutrient preparation.
Such benefits underscore the pivotal role of automation in modern hydroponic practices.
Essential Components Needed
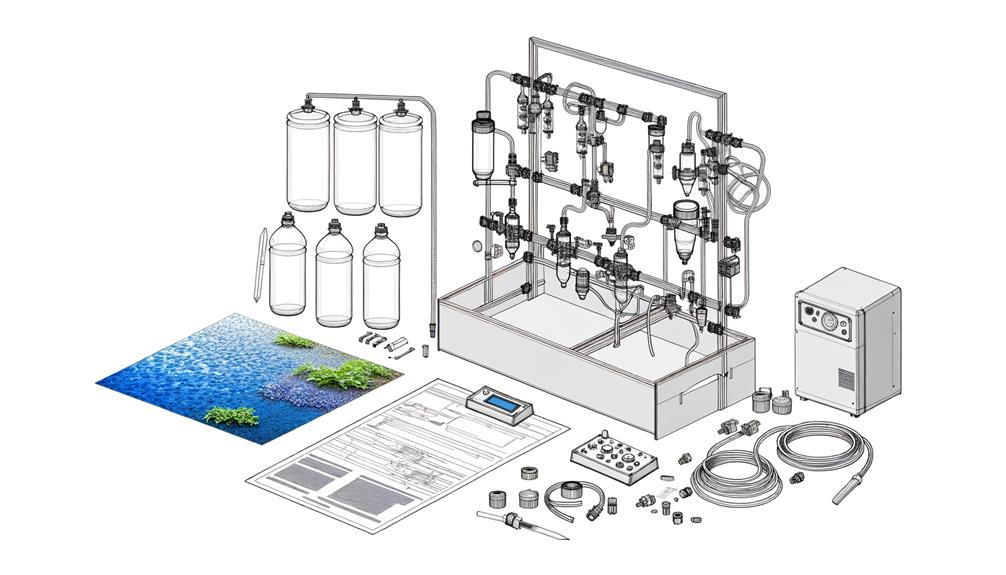
To construct an effective automatic hydroponic nutrient doser, one must procure several critical components including dosing pumps, nutrient reservoirs, and a reliable control system.
Dosing pumps, typically peristaltic or diaphragm, guarantee accurate and consistent nutrient delivery. Nutrient reservoirs, constructed from food-grade materials, store the essential nutrient solutions and should be appropriately sized to meet the system's demands.
A reliable control system, often a microcontroller or programmable logic controller (PLC), integrates sensors and actuators to automate nutrient dosing schedules and maintain peak nutrient levels.
Additional components may include pH and EC sensors for real-time monitoring, tubing for nutrient transfer, and mixing stations to guarantee homogenous nutrient distribution.
Together, these components guarantee efficient and precise nutrient management in hydroponic systems. This ensures that plants receive the optimal balance of essential elements for healthy growth and maximum yield. Following the 5 steps to mix nutrients correctly helps maintain solution stability and prevents deficiencies or toxicities. Proper monitoring and adjustments further enhance nutrient absorption and overall system efficiency.
Choosing the Right Pump
Selecting an appropriate pump for an automatic hydroponic nutrient doser requires careful consideration of both the pump flow rate and the material quality.
The flow rate must be sufficient to guarantee precise nutrient delivery, while the material quality must resist corrosion and chemical degradation from nutrient solutions.
Matching these specifications with the system's requirements assures operational efficiency and longevity.
Pump Flow Rate
Determining the appropriate pump flow rate is critical for ensuring the precise delivery of nutrients in an automated hydroponic system. Selecting a pump with an inadequate flow rate can lead to nutrient imbalances and compromised plant health.
A detailed analysis of system requirements, including the volume of nutrient solution and the frequency of dosing, is essential.
Use the following considerations to choose the right pump flow rate:
- System Volume: The total volume of the hydroponic system dictates the required pump capacity.
- Dosing Frequency: Higher frequency dosing may necessitate a higher flow rate.
- Nutrient Concentration: Different nutrients require specific flow rates for ideal absorption.
- Pump Head: The vertical distance the pump must move the solution impacts the flow rate.
Pump Material Quality
After establishing the appropriate pump flow rate, it is essential to contemplate the material quality of the pump to guarantee durability and compatibility with nutrient solutions.
Pumps used in hydroponic systems must resist corrosion and chemical degradation. Commonly, materials such as high-density polyethylene (HDPE), polyvinyl chloride (PVC), or stainless steel are preferred due to their resilience and inert properties.
HDPE and PVC are lightweight and cost-effective, ideal for standard nutrient solutions. Stainless steel, although more expensive, offers superior strength and resistance to a broader range of chemicals, making it suitable for advanced or variable nutrient mixes.
Ensuring the pump material aligns with the chemical properties of the solutions used will prevent premature failure and maintain system efficiency.
Setting Up the Control System
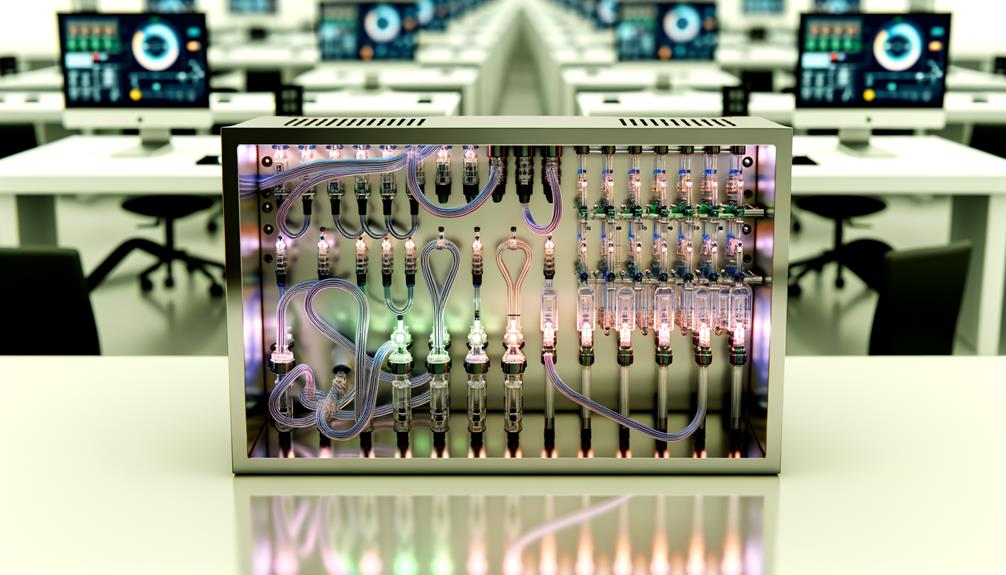
To establish an effective control system for your DIY automatic hydroponic nutrient doser, integrating a microcontroller like the Arduino or Raspberry Pi is paramount. This microcontroller will act as the brain, managing timing, nutrient levels, and pump operation.
Key components include:
- Sensors: Utilize pH, EC, and temperature sensors to monitor nutrient solution parameters accurately.
- Relays: Employ relays to interface the microcontroller with high-power devices such as pumps and solenoids.
- Power Supply: Guarantee a stable and sufficient power supply to avoid disruptions in the dosing schedule.
- Software: Develop or install robust software that can handle real-time data processing and control logic.
This setup guarantees precision and reliability in nutrient delivery.
Calibrating Your Doser
Proper calibration of the dosing system is critical to guaranteeing accurate nutrient delivery, which involves fine-tuning the sensors and pumps to match the specific requirements of your hydroponic setup.
Begin by verifying the accuracy of your pH and EC sensors using standard calibration solutions. Adjust the sensor readings in your control system to reflect these known values accurately.
Next, calibrate the dosing pumps by measuring the actual output against the expected volume. This can be achieved by running the pumps for a set time and measuring the dispensed liquid. Adjust the pump settings accordingly to guarantee precise dosing.
Regular re-calibration is recommended to account for sensor drift and pump wear, maintaining ideal nutrient concentrations for plant health.
Programming the Dosing Schedule
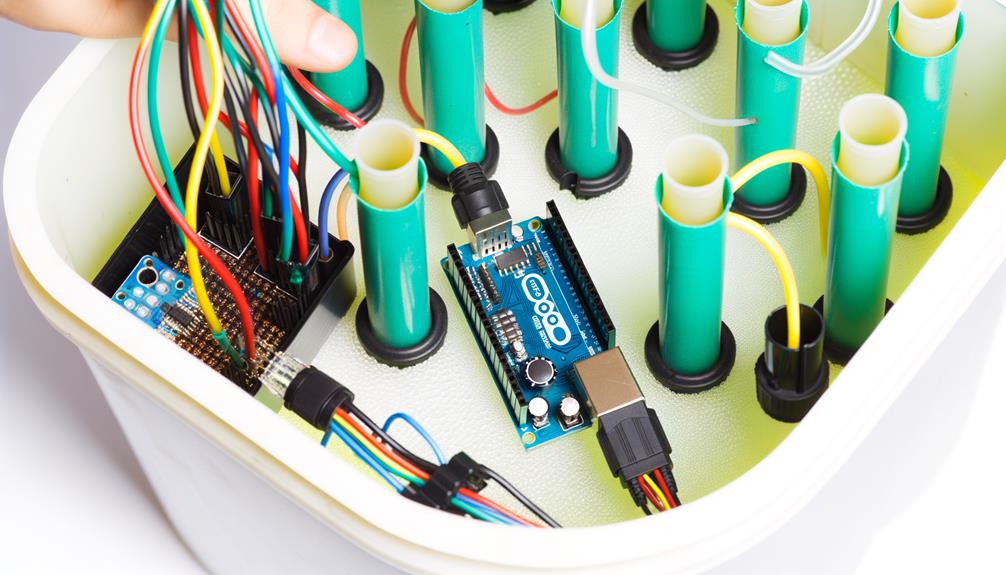
Establishing an effective dosing schedule requires a thorough understanding of your plants' nutrient needs at various growth stages and the specific parameters of your hydroponic system.
Begin by determining the ideal nutrient concentration for each growth phase—seedling, vegetative, and flowering. Utilize programmable timers or microcontrollers to automate the dosing intervals, guaranteeing precise delivery.
Integrate sensors to monitor and adjust for fluctuations in pH levels and electrical conductivity (EC) within the nutrient solution. Fine-tuning these parameters is essential for maintaining plant health and maximizing yield.
- Precision: Achieve unparalleled control over nutrient delivery.
- Consistency: Guarantee uniform nutrient distribution.
- Efficiency: Enhance resource usage and minimize waste.
- Scalability: Adapt the system to various plant types and growth stages.
Testing and Troubleshooting
After configuring your dosing schedule, it is imperative to rigorously test the system to identify and resolve any potential issues that could compromise nutrient delivery.
Begin by verifying that solenoid valves, peristaltic pumps, and sensors are functioning within specified tolerances.
Utilize a calibrated pH and EC meter to confirm that nutrient solutions are dispensed accurately.
Conduct a dry run to guarantee that there are no leaks or blockages in the tubing.
Inspect electrical connections to avoid short circuits or faulty wiring.
Simulate various scenarios to test the system's responsiveness and recalibrate as needed.
Document any anomalies and systematically address them to optimize system reliability.
This meticulous approach will guarantee consistent nutrient delivery and robust plant growth.
Maintenance and Upkeep
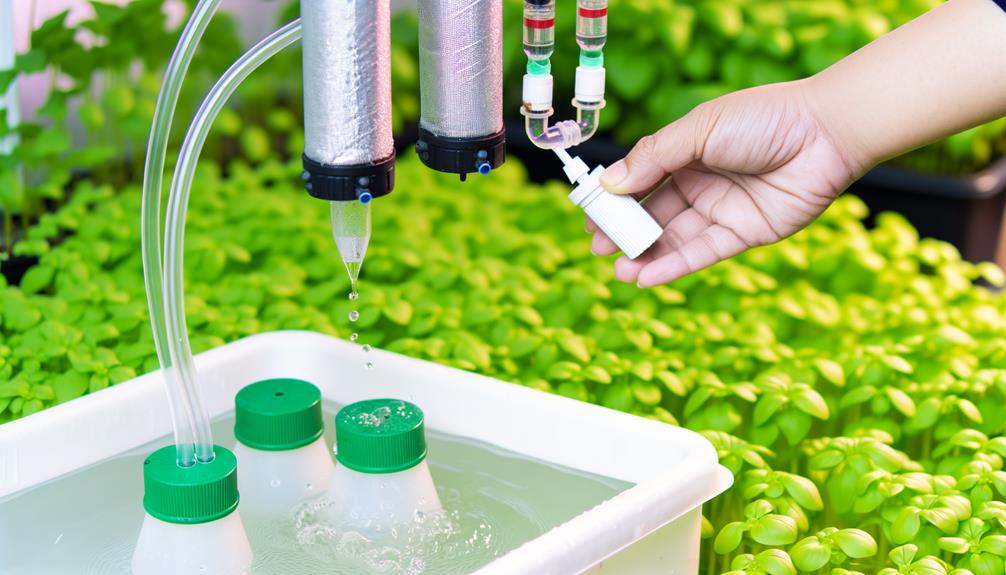
Routine maintenance and careful upkeep of your automatic hydroponic nutrient dosing system are critical for sustained performance and perfect plant health.
Regular inspection is paramount to guarantee the system operates without hitches. Key components such as pumps, tubing, and sensors should be routinely checked for blockages, leaks, and calibration drift. Nutrient solution reservoirs need periodic cleaning to prevent biofilm buildup and contamination.
Additionally, software updates for the control system should be applied promptly to enhance functionality and security.
- Prevent unexpected plant stress
- Avoid costly repairs and downtime
- Maximize nutrient delivery accuracy
- Guarantee ideal plant growth conditions
Conclusion
Much like a well-tended garden thrives under meticulous care, a hydroponic system flourishes with precise nutrient dosing.
An automated doser is the vigilant gardener, ensuring ideal conditions for plant growth. Through careful selection of components and meticulous calibration, the system operates seamlessly.
This synthesis of technology and nature epitomizes the future of efficient agriculture, embodying precision and reliability. Consequently, the automated hydroponic nutrient doser stands as a paragon of modern cultivation methods.