7 Steps to Building Ship Crate Hydroponic Systems
Building ship crate hydroponic systems requires precise construction using high-density polyethylene (HDPE) or food-grade plastic crates with adequate drainage and structural integrity. Implement marine-grade stainless steel fasteners, UV-resistant PVC piping, and high-efficiency LED lighting.
Verify marine-grade electrical wiring and a robust filtration system are in place. Assemble the crate frame using marine-grade lumber and apply a marine epoxy coating.
Integrate a nutrient reservoir, submersible pump, and aeration system. Select fast-growing, hydroponic-friendly plants like lettuce, herbs, or tomatoes, and maintain ideal pH and nutrient levels.
Successful execution of these steps guarantees an efficient hydroponic system tailored for maritime conditions. Continue for deeper insights into maintaining effectiveness.
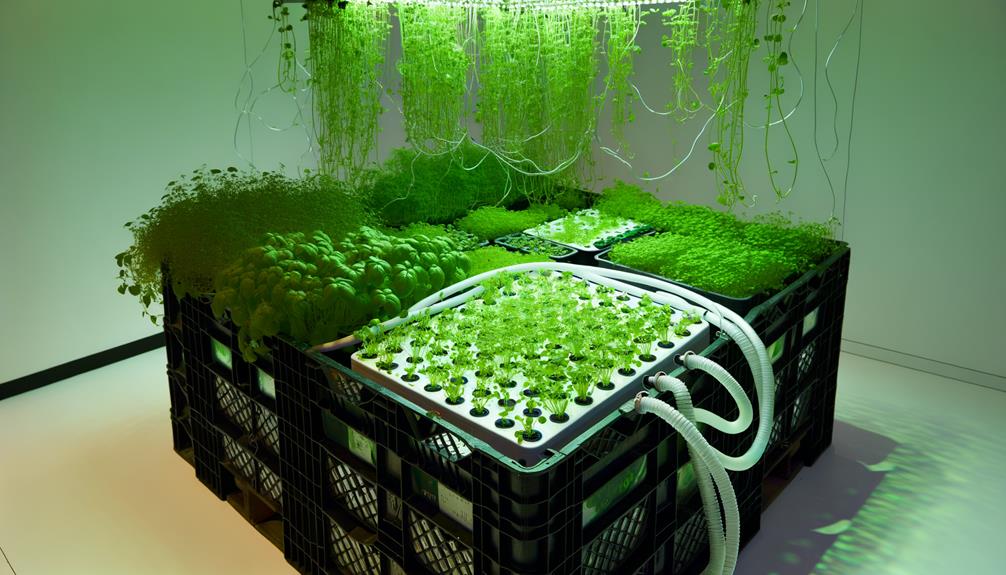
Key Takeaways
- Material Selection: Use high-density polyethylene (HDPE) crates for durability and food-grade safety.
- System Components: Include nutrient reservoirs, submersible pumps, grow trays, and aeration systems for efficient plant growth.
- Lighting Needs: Install high-efficiency LED lights with full spectrum for optimal plant development.
- Plant Selection: Choose fast-growing, low-light plants like lettuce and herbs for quick turnover and efficient space use.
Understanding Hydroponics
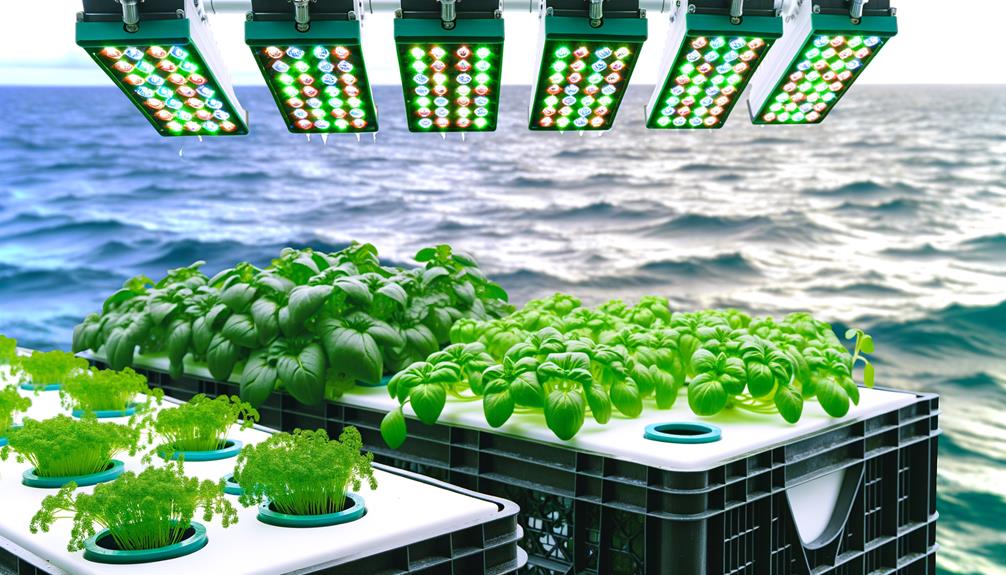
Hydroponics, frequently regarded as a revolutionary method of cultivating plants without soil, relies on a nutrient-rich aqueous solution to deliver essential minerals directly to the plant roots. This technique maximizes plant growth by eliminating soil-borne pathogens and enabling precise control over nutrient concentrations.
Employing hydroponics necessitates understanding the essential components: the nutrient solution, pH balance, and oxygenation. The nutrient solution must be meticulously formulated to include macronutrients (nitrogen, phosphorus, potassium) and micronutrients (iron, magnesium, calcium).
Maintaining an ideal pH range, typically between 5.5 and 6.5, guarantees nutrient availability. Additionally, assuring adequate oxygenation of the root zone prevents root hypoxia.
This method is particularly advantageous for environments with limited arable land, promising enhanced yield and resource efficiency.
Choosing the Right Crate
Selecting the appropriate crate for a ship-based hydroponic system involves considering factors such as material durability, size compatibility, and drainage efficiency. Confirming the crate meets these criteria will optimize plant growth and system longevity.
When choosing a crate, focus on:
- Material Durability: Opt for high-density polyethylene (HDPE) or food-grade plastic to withstand the marine environment and prevent chemical leaching.
- Size Compatibility: Confirm the crate dimensions align with the spatial constraints of the ship and the hydroponic setup.
- Drainage Efficiency: Select crates with adequate perforation to facilitate proper water flow and prevent root rot.
- Structural Integrity: Verify that the crate can support the weight of the hydroponic medium and plants, confirming stability during maritime operations.
These considerations are pivotal for an efficient hydroponic system onboard a ship.
Necessary Tools and Materials
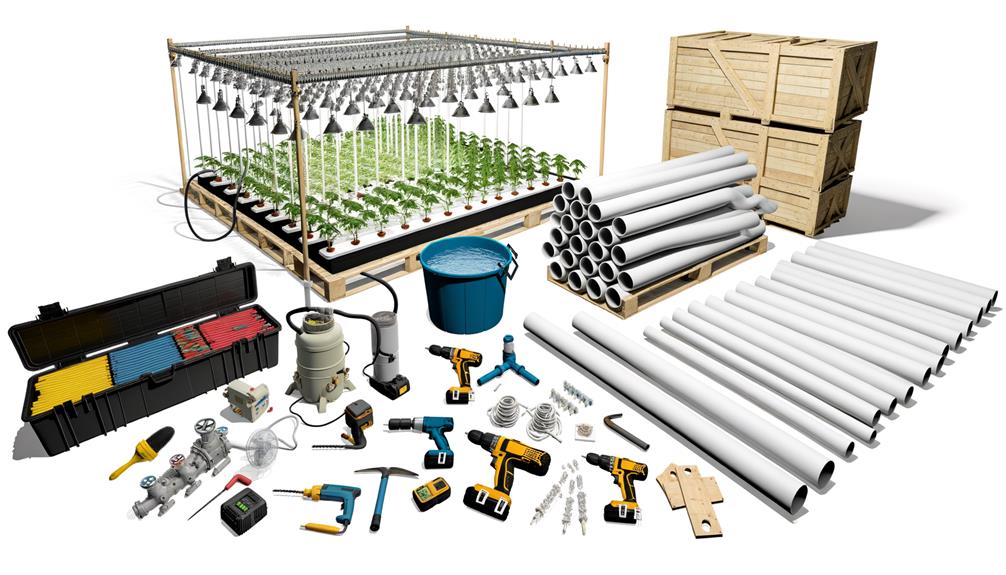
After securing the appropriate crate, assembling an efficient ship-based hydroponic system requires an extensive set of tools and materials designed for maritime conditions. Essential tools include stainless steel fasteners to withstand corrosion, marine-grade electrical wiring for safe power distribution, and a robust filtration system to guarantee water purity. Materials like UV-resistant PVC piping, moisture-proof insulation, and high-efficiency LED grow lights are critical. The following table outlines key components:
Component | Specification | Purpose |
---|---|---|
Stainless Steel Fasteners | Marine Grade | Prevents corrosion |
UV-Resistant PVC Piping | Schedule 40 | Durable fluid transport |
High-Efficiency LED Lights | Full Spectrum | Ideal plant growth |
Marine-Grade Electrical Wiring | Waterproof | Safe power distribution |
This guarantees resilience against harsh maritime environments, enhancing system longevity and performance.
Setting Up the Crate
Initiating the setup of the crate involves securing the structural framework to confirm stability and durability under maritime conditions. Begin by selecting high-grade marine plywood and corrosion-resistant fasteners.
Follow these steps meticulously:
- Frame Assembly: Construct the base and vertical supports using marine-grade lumber, confirming all joints are reinforced with stainless steel brackets.
- Waterproofing: Apply a marine epoxy coating to all wooden surfaces to prevent water infiltration and degradation.
- Ventilation: Integrate vent slots into the side panels to facilitate adequate air circulation, essential for maintaining ideal internal humidity levels.
- Insulation: Line the interior with reflective insulation to stabilize internal temperatures, mitigating the effects of external maritime climates.
These measures will confirm the crate's robustness, setting a solid foundation for the hydroponic system.
Installing the Hydroponic System
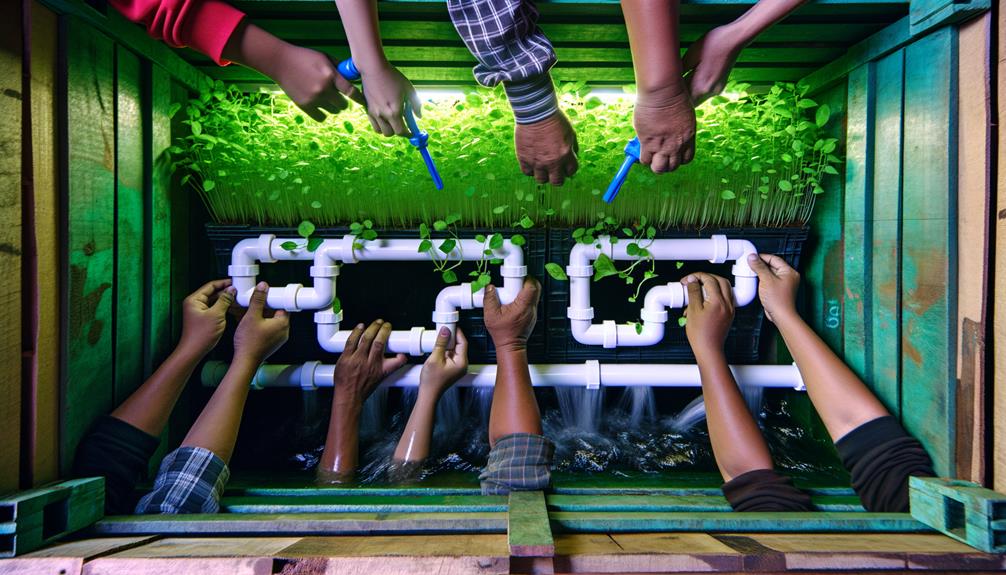
With the crate’s structural integrity and environmental controls firmly established, the next step involves meticulously installing the hydroponic system components to confirm ideal plant growth conditions. Begin by setting up the nutrient reservoir, making sure it is both leak-proof and appropriately sized. Connect the submersible pump to the delivery lines, which should be arranged to evenly distribute nutrient solution. Install the grow trays at a slight incline for best drainage. Finally, integrate the aeration system to maintain dissolved oxygen levels. To build a hydroponic system successfully, ensure that the pH and nutrient levels in the reservoir are regularly monitored and adjusted as needed. Position grow lights strategically to provide sufficient illumination for all plants, simulating optimal sunlight exposure. Lastly, implement a reliable timer system to automate nutrient delivery and lighting cycles, promoting consistent plant development.
Component | Description |
---|---|
Nutrient Reservoir | Leak-proof, appropriately sized container |
Submersible Pump | Connect to delivery lines for nutrient flow |
Grow Trays | Slightly inclined for effective drainage |
Aeration System | Maintains dissolved oxygen levels |
Precision in each step guarantees system efficiency and plant health.
Selecting Plants for Hydroponics
Selecting appropriate plant species for hydroponic systems involves evaluating the ideal hydroponic plant types, analyzing growth rate variations, and determining specific light and nutrient requirements.
Vital considerations include the adaptability of plants to a soilless environment and their compatibility with the hydroponic infrastructure.
Attention to these factors guarantees efficient resource utilization and maximizes yield potential.
Best Hydroponic Plant Types
Identifying suitable plant types for hydroponic systems involves evaluating factors such as growth rate, root structure, and nutrient requirements to guarantee ideal yield and system efficiency. Certain plants are particularly well-suited for hydroponic environments due to their adaptability and performance.
Key considerations include:
- Lettuce and Leafy Greens: Rapid growth cycles and shallow root systems make them ideal for hydroponics.
- Herbs: Basil, mint, and cilantro thrive with minimal nutrient demands and provide high-value yields.
- Tomatoes: Require more support and specific nutrient mixes but offer substantial yield per plant.
- Strawberries: Benefit from controlled environments, leading to consistent, high-quality fruit production.
Selecting these plant types can optimize system performance while ensuring sustainability and high output in ship crate hydroponic systems.
Growth Rate Considerations
Evaluating the growth rate of potential hydroponic plants is essential for ensuring system efficiency and maximizing yield within the constraints of ship crate environments.
Selection criteria should include germination speed, maturation time, and continuous harvest potential. Fast-growing leafy greens like lettuce and spinach, which mature in 30-45 days, are ideal for quick turnover. Conversely, slower-growing plants like tomatoes, requiring 60-85 days, necessitate strategic planning.
Evaluating root system development is important; compact roots prevent overcrowding. Additionally, plant height and spatial orientation must be considered to optimize vertical space utilization in ship crates.
Integrating data-driven growth models and leveraging genetic advancements can further enhance crop selection, ensuring high yield and system sustainability.
Light and Nutrient Needs
Understanding the specific light and nutrient requirements of hydroponic plants is crucial for maximizing growth conditions and guaranteeing maximum productivity within ship crate systems.
To select suitable plants, consider the following criteria:
- Light Intensity: Determine the photosynthetically active radiation (PAR) levels necessary for each plant species. High-light plants like tomatoes require 500-700 µmol/m²/s, while low-light plants like lettuce need 200-400 µmol/m²/s.
- Nutrient Concentration: Use electrical conductivity (EC) to measure nutrient solution strength. Leafy greens thrive at 1.2-1.8 mS/cm, whereas fruiting plants need 2.0-2.5 mS/cm.
- Photoperiod: Adapt light cycles to plant types; short-day plants (e.g., strawberries) need <12 hours of light, while long-day plants (e.g., spinach) require >12 hours.
- pH Levels: Maintain ideal pH levels, typically 5.5-6.5, to guarantee nutrient availability and uptake.
Maintaining Your System
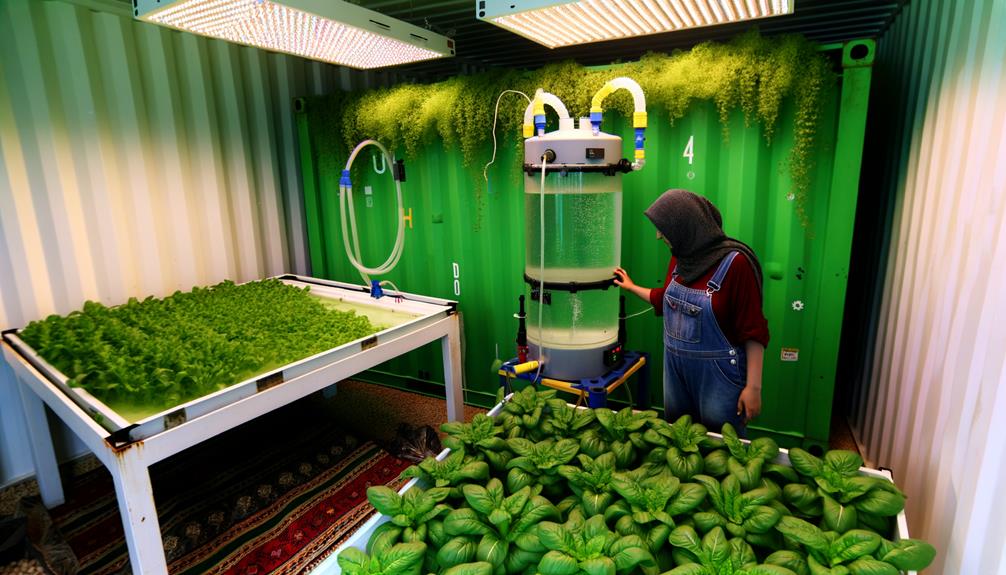
Maintaining your ship crate hydroponic system involves meticulous attention to regular nutrient checks and stringent cleanliness protocols.
Accurate monitoring of nutrient levels is critical to guarantee peak plant growth, requiring the use of precise measurement tools and calibration standards.
Additionally, implementing a routine cleaning schedule and utilizing appropriate sterilization techniques will mitigate the risk of pathogen build-up and system contamination.
Regular Nutrient Checks
Consistent monitoring of nutrient levels is critical to guaranteeing the ideal growth conditions within your ship crate hydroponic system. Proper nutrient management requires precise calibration and regular checks to avoid deficiencies or toxicities.
Implement the following protocol for superior nutrient maintenance:
- Daily pH Testing: Adjust to maintain a pH range of 5.5 to 6.5 for ideal nutrient uptake.
- Weekly Electrical Conductivity (EC) Measurement: Verify EC levels are within the specific range for your plant species to avoid nutrient imbalances.
- Biweekly Nutrient Solution Replacement: Prevent the build-up of unused nutrients and contaminants.
- Monthly Thorough Water Analysis: Conduct detailed tests for macro and micronutrient concentrations to adjust the nutrient formula accurately.
System Cleanliness Tips
Regular cleaning of your ship crate hydroponic system is essential to prevent pathogen proliferation and guarantee ideal plant health.
Begin by disassembling components such as nutrient reservoirs, tubing, and grow trays. Utilize a food-grade hydrogen peroxide solution (3-5%) to sterilize all parts. Scrub surfaces with a non-abrasive brush, ensuring biofilm removal. Rinse thoroughly with distilled water to eliminate residual chemicals.
For sustained cleanliness, implement a weekly maintenance schedule, including pH and EC meter calibration. Additionally, monitor for algal growth and promptly address any detected.
Employ inline filtration systems to reduce particulate buildup in nutrient solutions. Such meticulous maintenance preserves system integrity, optimizes nutrient uptake, and fosters robust plant growth, ultimately advancing your hydroponic innovation.
Troubleshooting Common Issues
Addressing common issues in ship crate hydroponic systems requires a methodical approach to diagnosing and resolving problems such as nutrient imbalances, pH fluctuations, and equipment malfunctions. To maintain ideal system performance, consider the following troubleshooting steps:
- Nutrient Solution Analysis: Regularly test nutrient levels to guarantee a balanced supply, adjusting concentrations to mitigate deficiencies and toxicities.
- pH Monitoring: Utilize precise pH meters to maintain a stable pH range, typically between 5.5 and 6.5, adjusting with pH up/down solutions as necessary.
- Root Health Inspection: Inspect roots for signs of rot or disease, guaranteeing adequate oxygenation and sanitation to prevent pathogen proliferation.
- Equipment Functionality Check: Routinely verify the operational status of pumps, timers, and aeration systems, repairing or replacing faulty components immediately.
Conclusion
The implementation of hydroponic systems within ship crates presents an innovative approach to urban agriculture.
A compelling statistic reveals that hydroponic systems can use up to 90% less water than traditional soil-based agriculture, highlighting their efficiency and sustainability.
By meticulously selecting appropriate materials, installing robust systems, and maintaining ideal conditions, significant advancements in plant cultivation can be achieved.
This method not only maximizes space utilization but also contributes to sustainable agricultural practices in urban environments.